PRODUCT DEVELOPMENT(R&D)
The process of mechanical product design typically involves the following steps:
1. Conceptualization: This is the earliest stage of the design process, where product designers identify the need for a new product or a redesign of an existing one. At this stage, the design team may gather market research data, identify user needs, and brainstorm creative ideas for the product design.
2. Engineering analysis: Once a product concept has been developed, engineers evaluate the feasibility of the design. Critical assessments such as stress analysis, finite element analysis, and modeling may be conducted to determine if the product will function correctly.
3. Design Specification: All design requirements for the product are defined at this point. It is critical to detail features such as size, shapes, materials, etc.
4. Design Calculations: Mathematical formulas and calculations are used to determine the strength, power, dimensions, and properties of parts to keep the intended specifications in consideration.
5. Prototyping: Designers create model assemblies or physicals prototypes with components to assess in reality what looks theoretically approved.
6. Testing: Fully-fledged project testing ensures that various products meet all requirements. For example, aesthetic assessment, usability, efficiency and performance.
7. Refining: After the prototype has been tested, engineers refine the product to improve its usability, durability, and safety features.
8. Production: Once the finished product design is authorized after correction as well as editing, manufacturers bring it in mass production to be delivered to customers.
We have a team of professional engineers, trained according to Japanese and EU standards. They have worked for many years at large Japanese corporations such as DENSO, TOYOTA, HONDA, EU…we understand our customers that they need to any thing and we will meet professional product design services with the best QCD, offer breakthrough solutions, bring competitive value to customers, create the best products for society.
We are professional in the fields of product design Automotive, household appliances, food based on aluminum, steel, plastic materials…
We will provide professional solutions in 3D modeling, CAE, testing, confirmability, toleranve analysis, propotype, lab service.
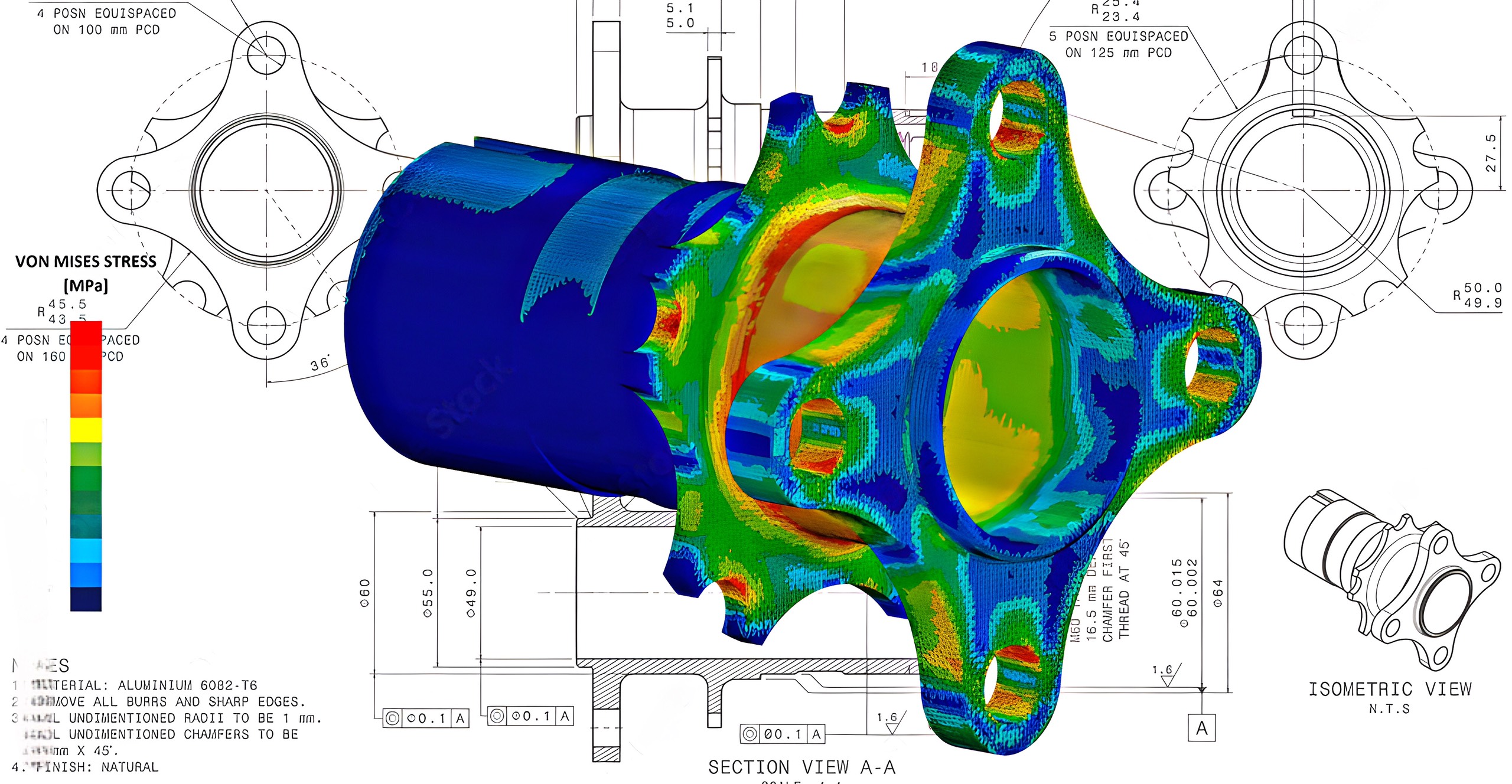
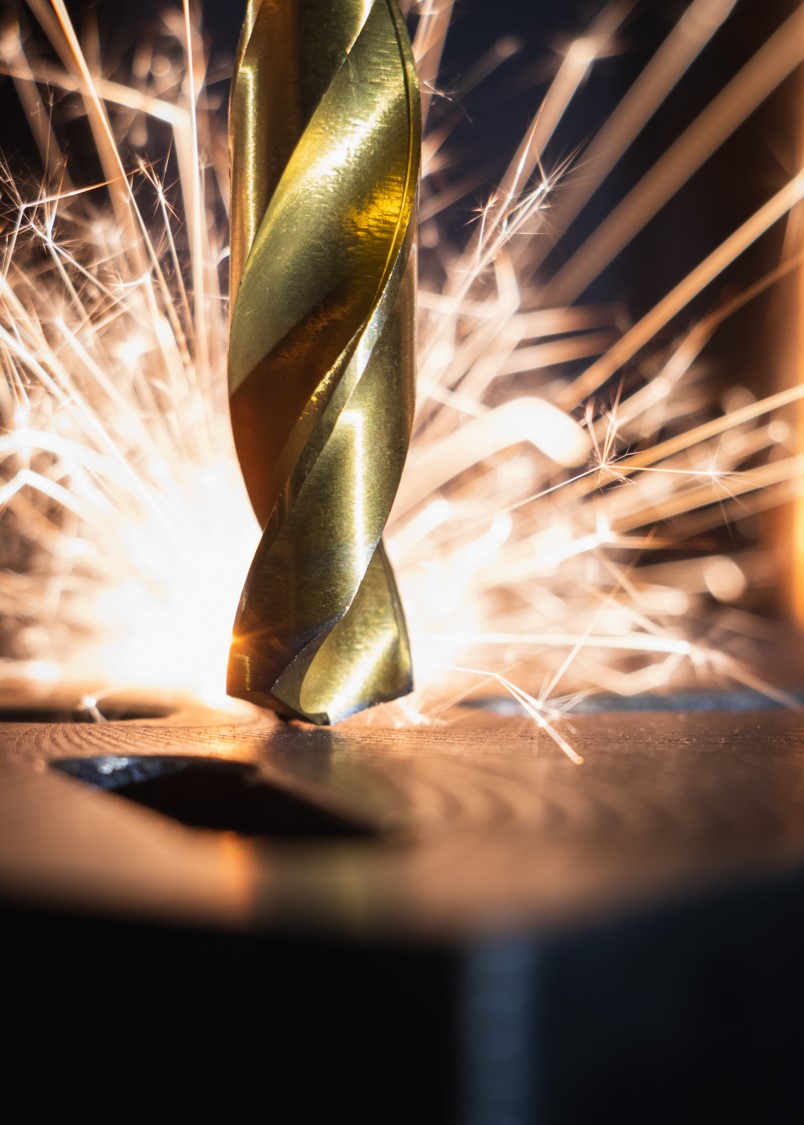
Design for X (DfX) is a general phrase that refers to designing products with specific objectives in mind. These objectives are focused on various aspects, which are mutually beneficial to producing simpler and more efficient product designs. Some of those aspects may include:
1. Design for Manufacturing (DfM): The purpose of DfM is to produce goods in a manner that is low cost, high efficiency and rapid production. By considering manufacturability early in the design process, design teams can improve quality and reduce waste throughout the manufacturing process.
2. Design for Assembly (DfA): DfA focuses on the aspects that enable expert assembly with a low cost and efficient speed. It helps to simplify product assembly, reduce assembly time, and associated costs by designing the product, keeping in mind its assembly requirements.
3. Design for Serviceability (DfS): DfS focuses on regular pro-active maintenance as well as repairs. Factors like enabling easy accessibility to defective parts in the repair work goes into designing for serviceability.
4. Design for Test (DfT): DfT is designed to simplify testing effectiveness, enhances system quality, and fast identification of the defects. The aim is to reduce cost while ensuring quality-inducing accessible testing structures.
5. Design for Safety (DfSI): DfSI involves risk management and product safety design to avoid hazards that could harm the users, property, or workplace during product use.
6. Design for Environment (DfE): DfE is a key consideration for companies. This aims to produce sustainable products that minimize the environmental impact, from issues such as carbon footprint, water contamination to waste management. DfX methodologies will improve the user experience by providing cost savings, diminished time to value, and superior product quality and requires some costs; however, investing in the designing for X approach will reap economical and business rewards over time.
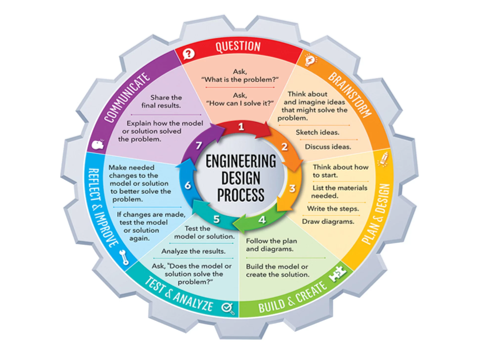
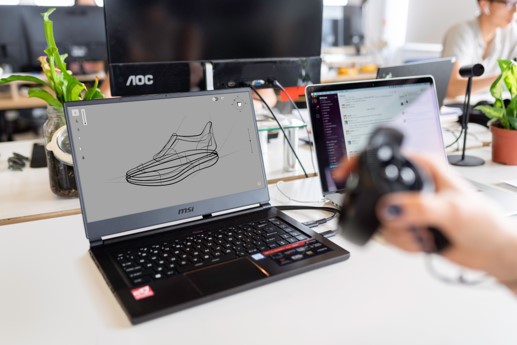